Product Categories
Hope Plastic Machinery
Rattan Extruder
This Rattan Extruder (Model: HPSJ-RA-01) is an intelligent manufacturing device equipped with a multi-screw collaborative extrusion system and a digital pneumatic material switching system. It supports eco-friendly materials such as PP, PE, and PVC, capable of producing round, flat, and tri-color/five-color gradient rattan strips. Since the launch of the first domestically developed model in 2002, the technology has undergone three iterations: from a single-color basic model (30kg/h) to a high-efficiency 60kg/h smart device integrated with a filter-brush dust removal system and modular dust collection units, reducing workshop PM2.5 levels by 75%. The current machine is tailored for weaving applications like rattan chairs and flower baskets, enabling 24/7 continuous production via hydraulic screen changers and unmanned winding systems. The products are SGS-certified for environmental compliance and feature UV resistance and exceptional weather durability.
Classification:
Production Process
Product Display
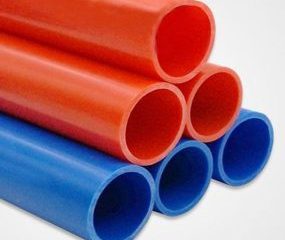
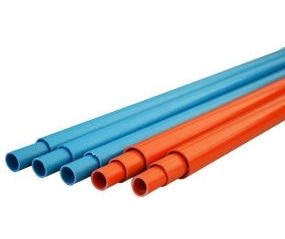
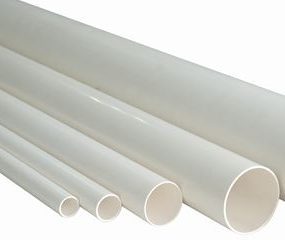
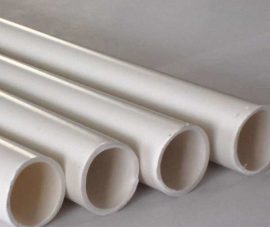
Production Line Composition
Extruder
Cooling System
Pulling System
Storage System
Product Introduction
Technical Background
Evolution and Innovations
As a pioneer in imitation rattan machine technology, we have driven industry advancements since 2002 with the following breakthroughs:
- Multi-color Composite Craft: Launched the “Fantasy Imitation Rattan Machine” in 2008, featuring a digital pneumatic material switching system for dynamic tri-color/five-color gradients and customizable cross-sectional shapes (round, flat, embossed, etc.).
- Energy-efficient Production: Low-melt-temperature plasticization technology boosts single-machine capacity to 60kg/h while cutting energy consumption by 33%.
- Eco-smart Systems: Integrated filter-brush dust removal and modular dust collection reduce PM2.5 by 75%, complemented by unmanned winding for uninterrupted 24-hour operation.
Core Advantages
- Material Versatility: Compatible with PP, PE, PVC, and anti-aging agent formulations, offering UV resistance and weather durability.
- Process Stability: Dual-screw extrusion ensures color uniformity; hydraulic screen changers eliminate downtime during material switching.
- Application Flexibility: Ideal for weaving rattan chairs, baskets, outdoor furniture, etc., with SGS-certified eco-friendly standards.
Structural Composition
Extruder:
- Screw and Barrel: The screw is responsible for plasticizing and extruding plastic raw materials. The barrel is usually made of high – temperature – resistant materials to withstand high – temperature and high – pressure environments.
- Motor: Drives the screw to rotate and provides the required power.
- Heating Device: Multi – stage heaters provide the required temperature control to ensure effective plasticization of plastics.
- Mold: A mold customized according to the pipe specifications is responsible for shaping the molten plastic into a pipe. The mold design affects the diameter and wall thickness of the pipe.
Product Parameters
Parameter | Value |
Extruder Model | HPSJ-RA-01 |
Applicable Materials | PVC, PE, PP, HDPE, PPR, ABS |
Tube Diameter Range | 50-200 mm |
Max. Output | 250-500 kg/h |
Screw Diameter | 50–75 mm |
Screw L/D Ratio | 25:1 |
Motor Power | 90 KW |
Max. Production Line Speed | 30 m/min |
Power Supply | 380V / 50Hz, three-phase (customizable) |
Product Features
High - Efficiency and Energy - Saving
Adopting advanced screw designs and optimized heating systems ensures rapid plasticization of raw materials, improves production efficiency, significantly reduces energy consumption, and supports green production.
Precise Temperature Control
The multi – zone temperature control system ensures stable temperature in each processing step, avoiding performance degradation of raw materials due to overheating or over – cooling, ensuring consistent pipe quality, and meeting the quality requirements of different customers.
Automated Operation
The equipment is equipped with a fully automatic PLC control system, which is easy to operate, monitors various production parameters in real – time, reduces human errors, and enables an efficient and stable production process.
Flexible Mold Configuration
It provides molds of various specifications and supports multi – layer co – extrusion technology, which can meet the requirements for pipes of different diameters, wall thicknesses, and layers, and easily handle customers’ personalized orders.
Application Fields
In 2023, the annual sales volume of our universal pipe extruders reached 10 units.
Hope Machinery has been deeply involved in the plastic extruder industry for many years, accumulating rich experience and professional knowledge, and has become a trustworthy partner for customers.
Through customer surveys, our customer satisfaction rate is as high as 95%, indicating the superiority of our products and services.
In the local pipe extruder market, our market share reaches 15%, showing strong competitiveness.