Product Categories
Hope Plastic Machinery
General Board/Sheet Extruder Production Line
The General Board/Sheet Extruder Production Line(Model: HPJX-BSE-01) is a widely used equipment for producing plastic sheets and plates, catering to industries such as packaging, advertising, construction, home appliances, and automotive. Through the extrusion process, plastic raw materials are heated, plasticized, and shaped via a die to produce sheets or plates of varying thicknesses, widths, and lengths. The machine supports processing of common plastics like PVC, PP, PS, ABS, PET, and PE. Key components include the extruder main unit, vacuum cooling water tank, belt haul-off machine, and high-speed cutting machine.
Classification:
Production Process
Production Line Composition
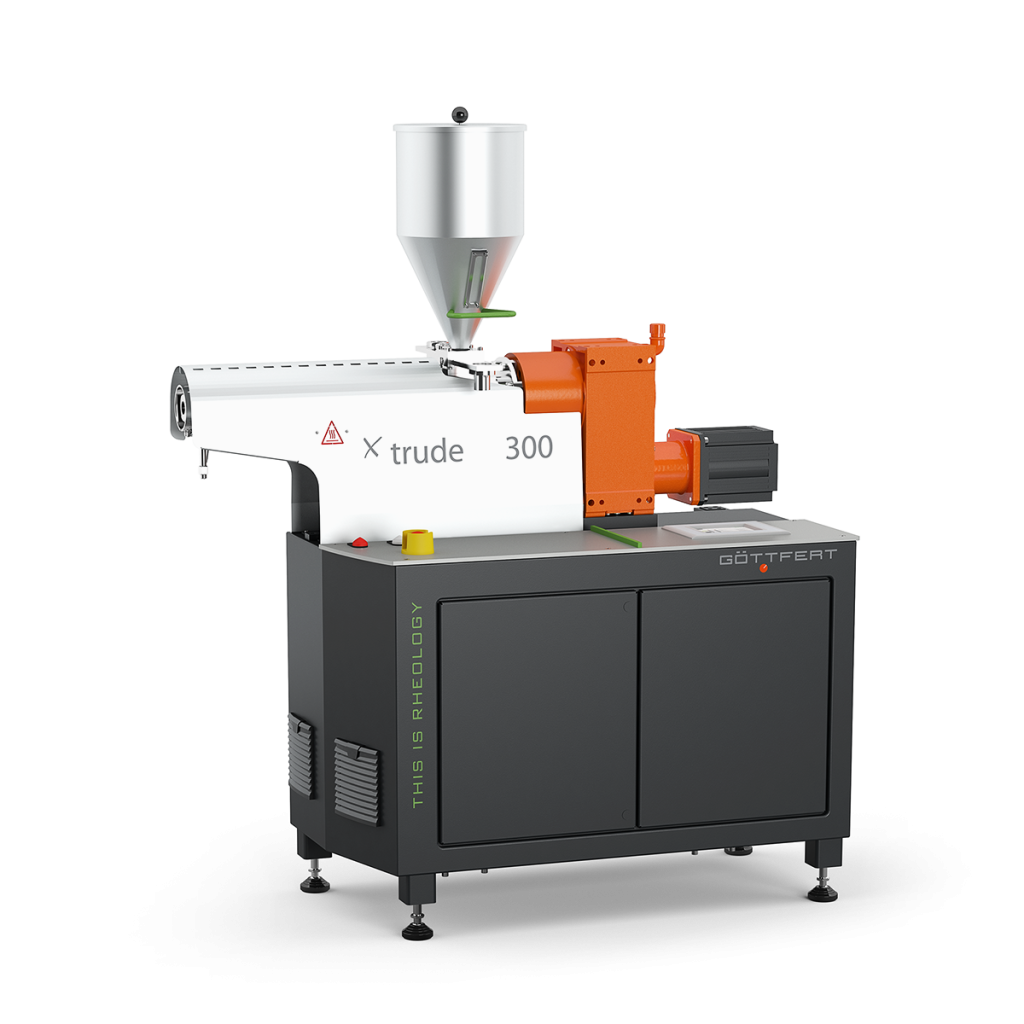
The extruder main unit is the core of the production line, responsible for efficiently plasticizing and extruding raw materials to ensure tubing quality and production efficiency. It features a high-precision screw and barrel design, paired with an advanced multi-zone temperature control system to guarantee stability and uniformity during extrusion. Driven by a powerful motor, the unit enables continuous, high-efficiency production and adapts to tubing of various specifications.
The cooling system is a critical component of the line, rapidly cooling and shaping extruded tubing to ensure dimensional stability and surface quality. It consists of stainless steel cooling water tanks and a precision-controlled cooling circulation unit.
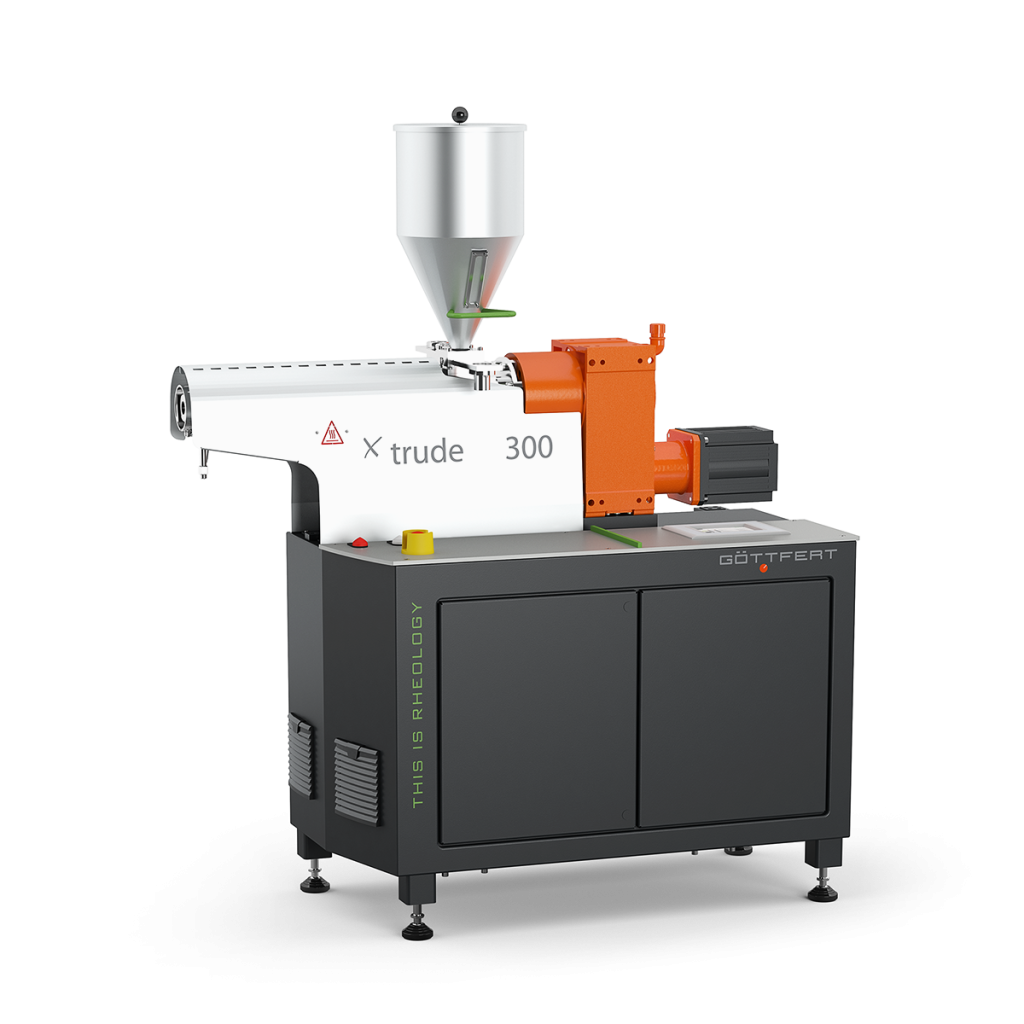
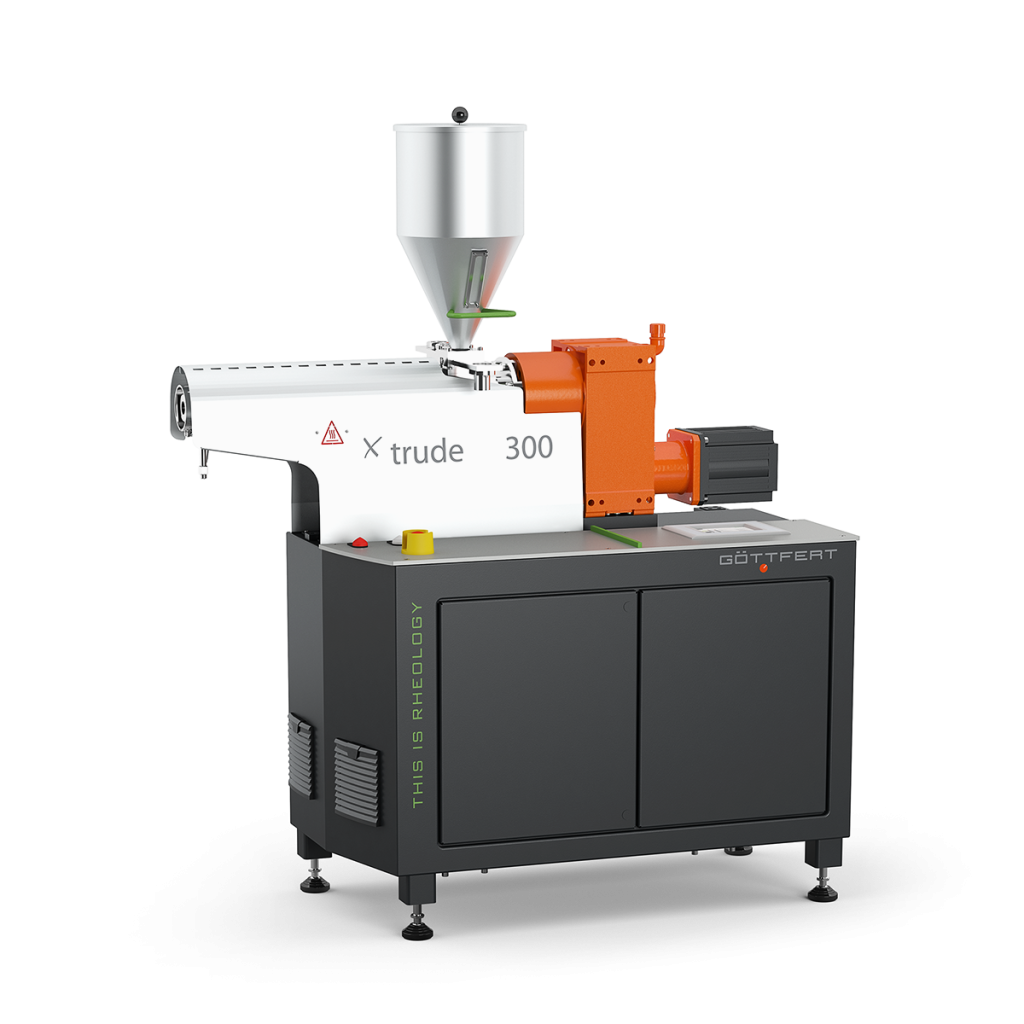
This system ensures stable pulling of the tubing from the cooling tank at a constant speed, maintaining dimensional accuracy and consistency. Equipped with multiple traction belts or pulleys and a precise speed control system, it accommodates tubing of varying specifications and wall thicknesses.
These final stages ensure seamless transition from production to packaging:
- Cutting System: Precisely cuts continuous tubing into preset lengths using high-accuracy blades.
- Collection System: Automatically coils or stacks cut tubing for organized storage and transport.
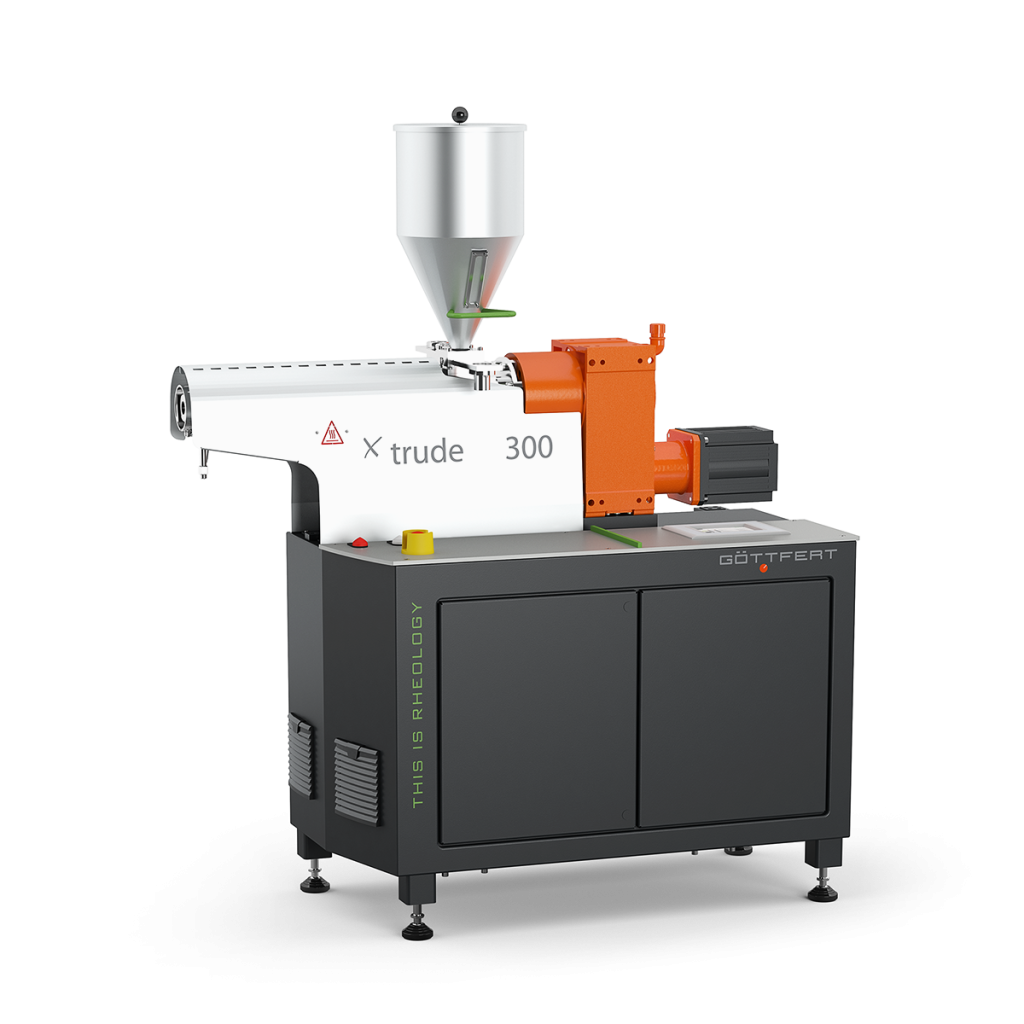
Product Introduction
Technical Background
The technological foundation of general board/sheet extruders originates from the plastic processing industry’s persistent demand for high-efficiency, multifunctional, and energy-saving equipment. Driven by rapid advancements in sectors such as packaging, construction, home appliances, advertising, and electronics, the market demand for plastic sheets and plates has surged. To address these industries’ stringent requirements for product quality, surface finish, dimensional precision, and production efficiency, universal sheet/plate extruders were developed and have undergone continuous technological innovation.
Traditional sheet production methods often grappled with inefficiencies, excessive material waste, and high energy consumption. In contrast, modern universal extruders achieve more efficient and stable production through three key advancements: precise temperature control, advanced screw plasticizing systems, and optimized die head designs. These machines process diverse polymer materials—including PVC, PP, PS, PET, and PE—enabling the manufacturing of sheets and plates with varying thicknesses and specifications. The integration of automated control technologies further enhances adaptability to diverse market demands, boosting production efficiency, reducing operational costs, and significantly elevating product competitiveness.
Furthermore, universal extruders increasingly incorporate energy-saving and eco-friendly innovations, such as high-efficiency drive systems and low-energy heating units, ensuring more sustainable and efficient operations. These technological advancements not only drive intelligent and automated production processes but also establish greener, more sustainable manufacturing practices for the plastic sheet industry.
Structural Composition
Extruder:
- Screw & Barrel: Plasticizes and extrudes material; barrel made of high-temperature-resistant material.
- Motor: Powers screw rotation.
- Heating System: Multi-zone heaters for precise temperature control.
- Die: Custom molds for shaping molten PVC into tubing (diameter/wall thickness).
Cooling System:
- Cooling water tank, circulation pump.
Traction System:
- Traction belts/pulleys, speed regulator.
Cutting System:
- High-precision blades, synchronized control.
Collection System:
- Automatic coiling or stacking platforms.
Product Parameters
Parameter Name | Value |
Extruder Model | HPJX-BSE-01 |
Applicable Materials | PVC, PS, PP, PE, PET, PMMA, PC, ABS |
Sheet/Plate Thickness Range | 0.3mm – 15mm |
Max. Output | 200 kg/h / 300 kg/h / 500 kg/h |
Screw Diameter | 65mm / 80mm / 100mm |
Screw L/D Ratio | 25:1 / 28:1 |
Motor Power | 30 kW / 45 kW / 75 kW |
Temperature Control Zones | 4-6 zones |
Max. Line Speed | 5-20 m/min |
Cooling Method | Water + Air Cooling |
Haul-Off Type | Belt/Roller |
Cutting Method | Planetary/Chip-free Cutting |
Coiling Method | Automatic/Manual (Customizable) |
Product Features
High - Efficiency and Energy - Saving
Adopting advanced screw designs and optimized heating systems ensures rapid plasticization of raw materials, improves production efficiency, significantly reduces energy consumption, and supports green production.
Precise Temperature Control
The multi – zone temperature control system ensures stable temperature in each processing step, avoiding performance degradation of raw materials due to overheating or over – cooling, ensuring consistent pipe quality, and meeting the quality requirements of different customers.
Automated Operation
The equipment is equipped with a fully automatic PLC control system, which is easy to operate, monitors various production parameters in real – time, reduces human errors, and enables an efficient and stable production process.
Flexible Mold Configuration
It provides molds of various specifications and supports multi – layer co – extrusion technology, which can meet the requirements for pipes of different diameters, wall thicknesses, and layers, and easily handle customers’ personalized orders.
Perfect Cooling and Pulling Systems
The high – efficiency cooling system and precise traction equipment ensure that the pipes maintain stable dimensions and smooth surfaces during the cooling and shaping processes.
Application Fields
In 2023, the annual sales volume of our universal pipe extruders reached 10 units.
Hope Machinery has been deeply involved in the plastic extruder industry for many years, accumulating rich experience and professional knowledge, and has become a trustworthy partner for customers.
Through customer surveys, our customer satisfaction rate is as high as 95%, indicating the superiority of our products and services.
In the local universal pipe extruder market, our market share reaches 15%, showing strong competitiveness.